
Why Emergency Stop Buttons Don't Prevent Accidents
Emergency stop buttons (e-stops) are something that most people are familiar with and have an understanding of, due to the extreme simplicity of the concept of having a button that stops all machine function. It is interesting to see the import that many people place on these safety controls, including people attributing injuries from an accident to the lack of having an emergency stop button. This issues of Clues will take a look at the benefits and limitations of emergency stop buttons, as well as what some standards say about the issue.
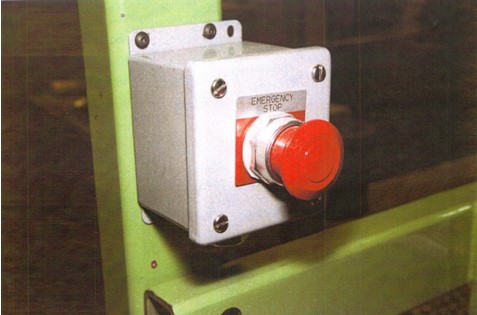
Why Doesn’t an Emergency Stop Button Prevent Accidents?
Emergency stop buttons are a method of last resort. A concept that eludes many intelligent people is that an emergency stop button will not prevent any accident. Some people may think that they would be able to hit an emergency stop at the exact instance that something goes wrong or an accident is beginning to occur. The reality of the situation is that as humans we have reaction time, which is the delay between awareness of something and being able to take action. The length of time it takes humans to perceive something then react takes anywhere between 0.5 seconds to several seconds, and it depends on variables such as expectancy of a situation and severity of a situation, as well as the number of possible reactions. The reality is in an accident, normally the harm is going to already have been done by the time the victim or a bystander can perceive, process, and react to a situation. There can be some exceptions to this, including someone caught in a machine that continues to cause harm of death to the individual, in which case an emergency stop could actually help to reduce the extent of injuries. Even in this case, the emergency stop should not be the primary safeguard, and the fact that someone is able to become entangled in the machine indicates a design failure or safety system failure. But in most accidents, the harm is done in a very short amount of time, and no human would be able to hit an emergency stop button in time for it to have an impact on the outcome of an accident. A relevant example from our everyday lives is getting hit by another vehicle, then honking the horn after the fact—the harm is already done. Modern guarding solutions can normally be used to safeguard machine and product hazards, ensuring no possible contact with a hazard. In theory, an emergency stop could prevent an accident in situations where a coworker sees someone about to enter a hazard zone, if a maintenance worker is in a hazardous point and the machine was not locked out and is accidentally energized, or if there is some malfunction to the machine that creates additional, unforeseen hazards. There are also machines that cannot always have every hazard guarded due to the hazards being part of the function of the machine, and emergency stops can make sense in these applications.
When is an Emergency Stop Button Appropriate?
They should never be used as a primary or secondary form of safeguarding. Emergency stops should never be used instead of proper machine safeguarding. Emergency stops may help minimize injuries if the emergency stop can be triggered in sufficient time, and there is entanglement without braking, or a continuous pressure or other hazard. Designers must focus on preventing accidents, instead of minimizing harm in the event of accidents – this is the responsibility of engineers – to fulfill their professional obligation to protect the health, welfare, and safety of the public.
If a designer does use an emergency stop as a backup system, the button must be placed so that the operator can reach the button while caught in the machine. The direction of button engagement must also be considered. An emergency stop button will be useless if the machine operator can reach the button but cannot engage it due to direction of engagement. For example, an emergency stop system that is guarding an in-running nip point should be configured so that the operator could pull the emergency stop while being sucked into the machine. A push button that the operator must engage while being pulled away from the button will not likely be engaged by the operator. Emergency stop buttons should also be configured so that bystanders can stop the machine in the event that the operator becomes trapped in the machine.
Situations where an emergency stop button could influence the outcome of an accident include high-powered machinery that have the potential to continue to harm either through rotational energy, pressure, heat or electrical energy. Again, even in these situations there should have been a primary safeguarding system that would have prevented the incident, but there are failures of primary safety systems either due to inadequate design, or safety system or component failure that is not failsafe. Body bars and similar limit switch devices could be considered a type of emergency stop, but these are automatically triggered if someone is pulled into a machine or crosses a threshold into a hazard zone, and do not require reaction on the part of an operator.
What do the Standards Say?
Different standards have different requirements for safety systems, including emergency stops, so each machine could have different requirements to comply with industry standards. ASME B15.1, Safeguarding of Mechanical Power Transmission Apparatus, Section 3.2.2.2.b states that “Emergency stop controls and/or warning signals shall not be used in lieu of guards or other positive safeguarding devices.” ANSI B11.19 states in section 7.2.4 “The interlocked guard(s) shall be prevented from opening until the hazard has ceased, or shall be located such that an individual cannot reach the hazard before cessation of the hazard when the interlocked guard is opened.” Many standards reference using a hazard assessment to identify hazards and assess safeguarding. While there is subjectivity to hazard assessments, they pivot around minimizing hazard, which is something an emergency stop button does not do, as in most applications there are more effective guarding solutions. Emergency stops are required on some machines such as conveyors where the rotational hazards and pinch points cannot always be guarded. Standards specific to certain machines will have specific requirements on safeguarding and e-stops.
How We Can Help? At MASE, we can determine if a product or machine is defective due to unguarded hazards or lack of adequate safety systems. We offer full service mechanical engineering expert witness services.