
Lockout / Tagout
What is Lockout / Tagout?
OSHA standard 49 CFR 1910.147 calls for the locking out of hazardous energy when an employee is exposed to potential machinery hazards during maintenance or servicing activities, which also include cleaning of machinery. Locking-out means exactly that, locking the power source in a de-energized state, with the key to the lock given to the person who will be exposed to the hazard. If there are multiple people exposed, there should be a lock for every person. Tagging-out involves the same concept, although with a tag instead of a lock, where the personnel exposed to the hazard each have a tag that they remove when completed with maintenance procedures. The OSHA Lockout/Tagout standard requires employers to use lockout unless it is not possible to do so, which makes sense as a lock is obviously much more secure than a tag that could be removed by anyone despite the tag having the person’s name written on it.
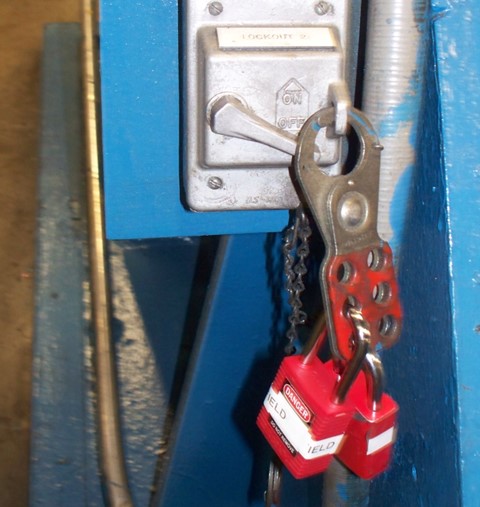
Main Power Supply to Entire Line Locked Out for Author's Inspection of a Machine Involved in an Accident
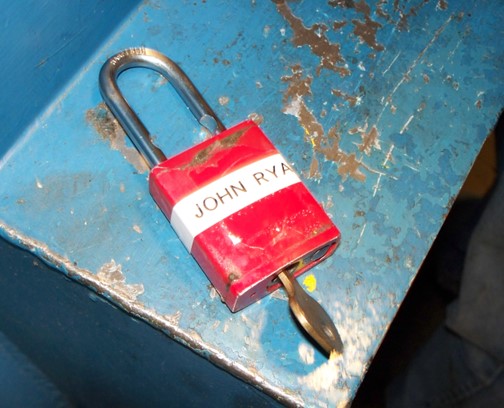
Author’s Lock for Machine Inspection
Why is Lockout / Tagout Necessary if the Manufacturer Conforms to Industry Standards?
There are hazards involved with maintenance activities that are not there with normal operation.
Different parts of the machine are being accessed during maintenance activities, that operators cannot
access, and therefore are not always guarded. Ideally, a manufacturer designs the machine with
maintenance and servicing procedures in mind, and builds into the machine safeguards that protect
maintenance workers, or at the very least, the ability to lockout the power to the machine. Machine
manufacturers can be held liable for injuries if they have not incorporated adequate safeguards not only
for operation but also maintenance. This can be overlooked by machine manufacturers, the end result
being the majority of machine guarding accidents the author has investigated occur during maintenance
operations.
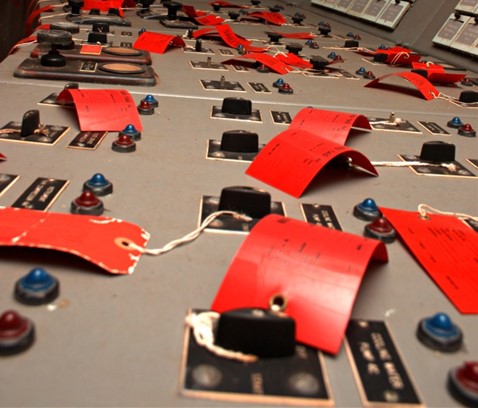
Example of Tagout (By Gregory Maxwell (User:Gmaxwell) - Own work, GFDL 1.2, https://commons.wikimedia.org/w/index.php?curid=153172)
What Does the Law Say?
“1910.147(a)(2)(ii)
Normal production operations are not covered by this standard (See Subpart O of this Part). Servicing and/or
maintenance which takes place during normal production operations is covered by this standard only if:
1910.147(a)(2)(ii)(A)
An employee is required to remove or bypass a guard or other safety device; or
1910.147(a)(2)(ii)(B)
An employee is required to place any part of his or her body into an area on a machine or piece of equipment
where work is actually performed upon the material being processed (point of operation) or where an associated
danger zone exists during a machine operating cycle.
1910.147(c)(1)
Energy control program. The employer shall establish a program consisting of energy control procedures, employ
ee training and periodic inspections to ensure that before any employee performs any servicing or maintenance
on a machine or equipment where the unexpected energizing, startup or release of stored energy could occur and
cause injury, the machine or equipment shall be isolated from the energy source and rendered inoperative.
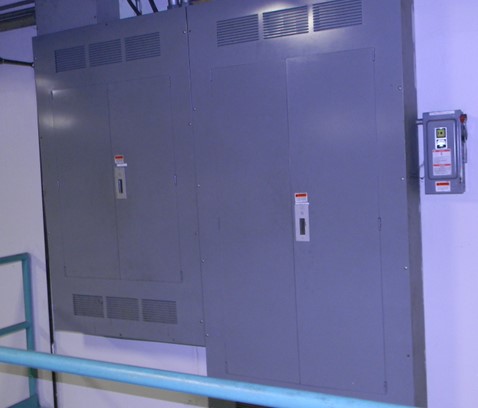
Main Power Supply to Entire Line Locked Out for Inspection
Brief Case Study
Product: Egg roller press
What happened: Worker cleaning machine gets sucked into powered rollers resulting in amputated fingers
Theory of liability: Machine failed to meet machine guarding standards
MASE expert: John Ryan
Result: Mediation trial Plaintiff win for undisclosed amount
How is Lockout / Tagout Relevant Here?
While the manufacturer was appropriately held responsible for failure to safeguard their machine for cleaning
operations, a lockout would have prevented this accident. A subtlety of cleaning rollers is the need to rotate the
rollers as the entire roller surface is typically not accessible. Locking out the machine would have made the
cleaning process significantly longer as the machine would have to be unlocked, started, rotate rollers, then locked
out again to clean the rollers, then repeated. Locking out also depends on human behavior to complete the
lockout process, which is often bypassed or skipped for time’s sake. Safeguards built into the machine are not
dependent upon user behavior, making it more effective, and a backup if an employer fails to use the locking out /
tagging out process.
How We Can Help? At MASE, we are licensed professional engineers, that can sift through the details of employer versus manufacturer
responsibility, as well as machine guarding defects versus a failure to lockout. We offer full service mechanical
engineering expert witness services.